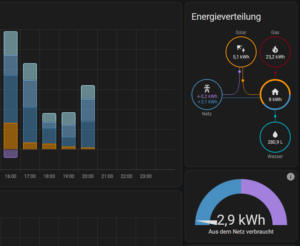
Emporia Vue 2 Custom Firmware
About a year ago, I found myself on the hunt for energy meters compatible with my power distribution box and stumbled upon Vue 2 by Emporia Energy. This device, with its support for three primary phases and 16 individual subnets, intrigued me. One of its...
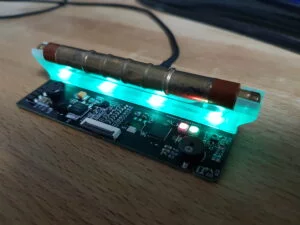
An IoT Geiger Counter
Building an ESP32 based geiger counter, for reporting radiation levels to a time series database, visualizing with grafana
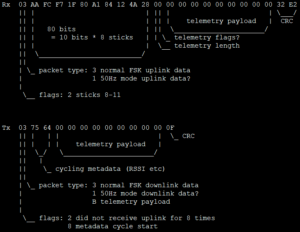
[FPV] Analysis of TBS Crossfire, reverse engineering the air link
I started flying FPV quads for a bit of freestyle flying about two years ago. Not very skilled, but also flying every now and then, so no real focused learning. Quickly I jumped onto the TBS Crossfire train and bought a TBS Tango 2 and...
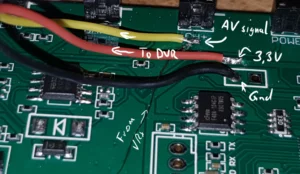
[FPV] Eachine EV800 mods
I own FPV goggles from Eachine and have been very happy with them. Yes, you look like an idiot with a brick on your forehead, but the antennas make you look more like a Johnny 5 fan, which is cool again. At least was 3...
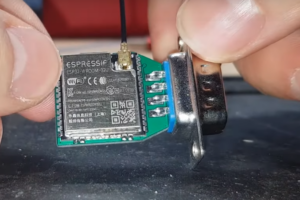
[ESP32] A tiny WiFi/BT to (true) RS232 adapter
Ages ago I received a defective Keithley SourceMeter 2400 that I could easily repair. I also have an old AOR A5000. Both are remotely controllable using their RS232 interface. But nowadays long RS232 cables aren’t quite state of the art and placing USB cables through...
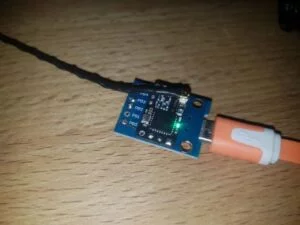
[ATtiny85] A simple TBS Crossfire USB adapter
Some time ago I built an aliexpress-part-based FPV quad and started flying around. Well… A few days later I had to buy the same parts again. Due to winds I totally lost control and the drone went out of range just while I hit the...
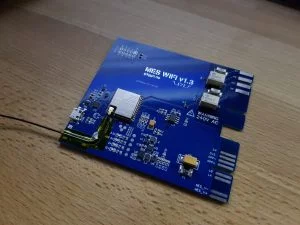
[MES-WiFi] Bringing a Windhager PMX150 pellet heater online
Since we own our house with a pellet heating system, it does its job day for day and delivers the warmth you’d expect from it. It rarely fails. Well, rarely. Except when I forget to refill the pellet container which has to be done every...
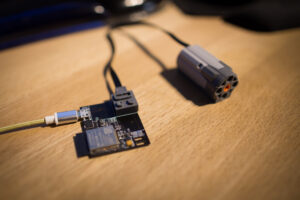
[ESP32] LegoRemote – a BLE/WiFi remote control for motors using a Steam Controller
Many years ago when I was young, I always wanted to have technic bricks to build some cool stuff with it. Self driving tanks, rotating cannons and shooting smaller bricks around. But back then I had no technic. Well, not even bricks. Just a friend...